Share
Pin
Tweet
Send
Share
Send

Steel springs can be of different configurations and it is not always possible to get the right type - the product is quite rare on the market. For this reason, for my needs, I make them myself.
What do we need
- Lathe and pipe of the desired diameter with a fixing bolt;
- Steel wire of the required diameter;
- Nippers;
- Thickness gauge;
- Reference engineer mechanical engineering for the calculation of springs;
- Calculator;
- Measuring compass, pencil, ruler and note paper.

Spring calculation

To do this, use the table in the spring section to correctly select the diameter of the steel wire, the number of turns and the pitch. At the same time, the way a new spring should work — compression or tension — plays a huge role. The latter type of springs can have a rather complicated design, but it can also be done independently. Having performed preliminary calculations and finding out the thickness of the wire for a steel spring, the pitch and number of turns, as well as determining the structural features and creating a drawing of the future spring, we can proceed to practical actions.

There is also special software for calculating all parameters:

Spring manufacturing
We have a drawing, a steel string of the required thickness and a suitable diameter, a steel tube for winding a spring.
Common mistakes
We clamp the mandrel in the lathe chuck. We insert the end of the steel wire into the hole in the mandrel, start the rotation and tightly wind the steel string.


After checking the thickness of the spring with a caliper, we cut the wire with wire cutters and observe how our spring grows in diameter.

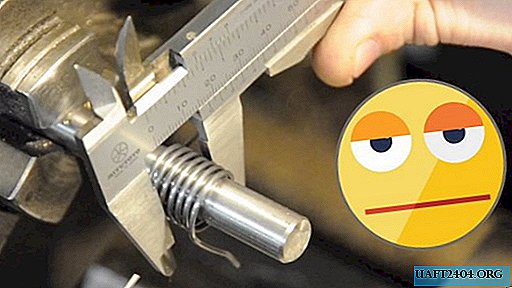
In addition, removing it from the mandrel will be quite problematic - for this you will have to cut the string at the very beginning of the turn.
Doing it right
Clamp the wire on the mandrel with a screw.

Now we need to create the tension of the steel string before winding.

Using a regular piece of thick plastic to pinch the wire in the tool holder will not be enough. We will need a special device with a guide, in which the wire tension can be adjusted by a pressure plate made of soft metal (copper or bronze).
It is also necessary to adjust the rotation speed of the lathe chuck and the movement of the working platform to obtain the desired spring pitch.
Winding

Slowly rotating the machine, we make the winding of the first two turns one to one - this is the beginning of our spring. Next, we activate the rotation with the movement of the working platform and perform the estimated number of turns.

At the end, we also make two tightly wound turns. Cut the wire with wire cutters and loosen the clamp bolt. Check the step using a ruler.

In a compression spring, we cut the remaining ends of the wire with pliers and grind the edges so that they become flat.



Making a double torsion spring

By learning how to make a normal tensile / compression spring, you can easily make a similar torsion element with your own hands. To do this, we clamp the wire on the mandrel, make the desired number of turns one to one and remove the winding from the tube. Using pliers, we attach the desired shape to the clamping bracket and again we put it on the mandrel with the free end. In this case, be careful that the direction of the turns coincides with the first winding. Make the same number of revolutions and bite off the finished product with pliers, leaving a couple of centimeters to fix the spring block.
Spring travel direction
In some cases, the direction of travel of the spring may matter - if two spring elements with different orientations are installed on the same site in a structure, this can lead to incorrect results.
Do not forget to use personal protective equipment and adhere to the rules of work on a lathe. As you can see, there is nothing complicated in the manufacture of spring elements, and if you have access to a lathe, you can always make them yourself.


Share
Pin
Tweet
Send
Share
Send